The plastic crisis is one that’s been rising exponentially throughout the several years. Because of this, it’s vital that alternative materials are to be looked at in order to find a solution for this issue. Several Japanese beverage vendors have recently moved to abandon the use of plastic bottles, replacing them with aluminium cans in a bid to combat marine plastic pollution, wreaking havoc with the ecosystem.
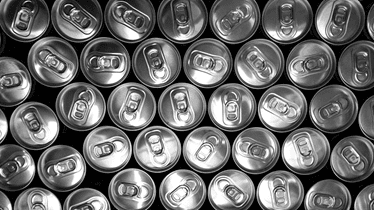
The rate of “horizontal recycling,” which allows for the reuse of materials in a comparable function, was substantially higher for such cans compared to plastic bottles. The rate of horizontal recycling for aluminium cans stands at 71.0 percent compared to 24.3 percent for plastic bottles, according to the Japan Aluminium Association and the Council for PET Bottle Recycling. Aluminium cans can better prevent their contents from deteriorating as their opacity keeps light from damaging them. Mineral water was supplied in aluminium cans at the Group of Seven summit in June in Britain, while consumer goods giant Unilever Plc said in April, it would begin selling shampoo in aluminium bottles in the United States.
The brand “Lifetime” announced that it will eliminate plastic water bottles at its over 150 locations in North America — all by September of this year. Aluminium bottles with Lifetime-branded natural alkaline spring water will replace plastic bottles. It’s a broader sustainability initiative, which focuses on reducing single-use plastics. According to data from the EPA, the brand’s decision to replace plastic water bottles with aluminium will help its sustainability profile from a recycling standpoint (aluminium is infinitely recyclable).
Over the past 100 years, plastics and polymers have changed the way the world operates, from airplanes and automobiles to computers and cell phones—nearly all of which are composed of fossil fuel-based compounds. A new plastic derived from pine sap has the potential to be a game changer for new sustainable materials. Glassy, thermally stable plastic can be melted and shaped at a higher temperature and cools into a hard plastic at ambient temperatures. This material has many structural features that mirror the plastics we use every day, so there is promise for a multitude of applications. “Ninety-nine percent of plastics today are produced from finite fossil fuels with increasing demand and limited geographic availability”. Pine sap, which may be harvested without killing the tree, is a noteworthy effort. Alpha-pinene, the most abundant molecule produced from pine sap, is notoriously difficult to turn into plastics so it currently has limited uses. Primarily found in turpentine-based cleaners and solvents. Researchers could control molecule growth, and how condition variability affected the materials. They also characterized the various material properties of the plastic, such as what temperature at which the polymer melts and how much heat it can withstand before it decomposes, as well as exploring the materials’ molecular structure. For this high-performance material, having a short shelf life from being biodegradable would be undesirable, but it still needs a way to be recycled. That may mean developing decomposition processes via a chemical stimulus.
Converting plastic bottles into vanillin using bacteria is another option to explore. The goal was to improve a process for converting plastic trash into protein powder and lubricants using a combination of chemicals and high heat (pyrolysis). The two scientists call their project a food ‘generator.’ Researchers envisage a system in which individuals may deposit plastic garbage or non-edible biomass into a slot. The waste goes into processing reactors where heat is used to break it down. The by-product is then put into a tank with a bacterial population, which feasts on it. The cells are then dried down into a powder and stored for subsequent use. The resulting foods “contain all the required nutrition, are nontoxic, provide health benefits and additionally allow for personalization needs. The researchers are experimenting with a range of PET materials to find the optimal particle size and processing parameters for reducing energy use while still producing the most product that will be eaten by the microbial community. The ground-breaking technique has the potential to provide a safe and sustainable food supply while decreasing the environmental harm caused by plastic waste and traditional farming practices.
Another group of researches had created a new biodegradable plastic which decomposes in sunlight and air. The researchers detailed their new environmentally degradable plastic that breaks down in sunlight into succinic acid, a naturally occurring non-toxic small molecule that doesn’t leave micro plastic fragments in the environment. The by-product of the plastic, succinic acid, could also be upcycled for commercial use in the pharmaceutical and food industries. Degradable plastic could be particularly useful in electronics. When in use, the plastic would be encased within the electronics device and would, therefore, be shielded from air and sunlight, allowing it to last for years. Once at a landfill, the device would be broken up and the plastics would likely be exposed to the sun, meaning they would decompose within days.
Finally, Researchers and scientists in Norway and Indonesia have taken big strides with regards to developing seaweed-based packaging, eschewing the need for plastic. The scientist, who is also co-founder and chief of research and development at Evoware, a sustainable packaging start-up, created the company’s bespoke red algae packaging. It can last up to two years and is also edible. So far, 200 companies across the food, cosmetics and textile industry have been testing said product. British start-up Notpla has developed a range of food and drink packaging that uses seaweed as its base. Co-Founder of Notpla, Pierre Paslier said: “Takeaway sauce sachets are one of the hardest single use plastics to deal with. As bioplastics go, seaweed makes for one of the best alternatives to conventional plastic packaging. Its cultivation is not based on land-sourced materials, it does not give any fodder to the usual dispute on carbon emissions. Also, seaweed does not require the use of fertilizers. It serves to restore the health of its immediate marine ecosystem and is not only biodegradable but also home compostable, meaning it does not need to be broken down via chemical reaction in an industrial facility.
REFERENCES
https://gearjunkie.com/news/twia-08-02-2021
https://phys.org/news/2021-07-sapbased-plastic-potential-gamechanger-future.html
https://interestingengineering.com/new-biodegradable-plastic-decomposes-in-sunlight-and-air
https://waste-management-world.com/a/seaweed-the-answer-to-the-plastic-crisis