In natural conditions, plastics are nearly indestructible, and yet they are discarded worldwide on a large scale: the world produces around 359 million tonnes of plastics each year. The main issue is not with plastic as a material, but with our linear economic model: goods are produced, consumed, and then disposed of. This model assumes endless economic growth and doesn’t consider the planet’s exhaustible resources. Plastics are strong, durable, waterproof, lightweight, easy to mould, and recyclable – all key properties for construction materials. Recycled plastics may have lower mechanical properties compared to virgin plastics, because each time you melt and process a plastic, the polymeric chains degrade. Any plastic waste can be shredded and used as filler for asphalt or be pyrolysed – decomposed through heating – to produce fuel.
The Japanese company Blest Corporation already sells a portable machine to convert domestic plastic waste into fuel in a simple, affordable way. Recycling much of plastic waste is currently unfeasible and unprofitable. Polymers such as rubbers, elastomers, thermosets and mixed plastic waste are comfortably labelled as “unrecyclable” by the recycling sector. From agricultural wastes such as sugarcane bagasse – a by-product of the sugar industry in Brazil – and coffee dregs, to concrete waste and construction debris, compounded with recycled plastics, there are many ways to obtain materials to produce bricks, roof tiles, plastic lumber and other useful elements for building. According to the Global Footprint Network, before the pandemic we were demanding 1.75 times the available resources of the planet. Working with the “unrecyclable” waste and developing plastics alternatives to natural materials may reduce this demand and leave a cleaner and more sustainable planet for the next generations.
A system developed in India, replaces 10% of a road’s bitumen with repurposed plastic waste. By 2040, there is set to be 1.3 billion tonnes of plastic in the environment globally. India alone already generates more than 3.3 million tonnes of plastic a year – which was one of the motivators behind incorporating waste into roads. It has the benefit of being a very simple process, requiring little high-tech machinery. Many different types of plastics can be added to the mix: carrier bags, disposable cups, hard-to-recycle multi-layer films and polyethylene and polypropylene foams have all found their way into India’s roads, and they don’t have to be sorted or cleaned before shredding.
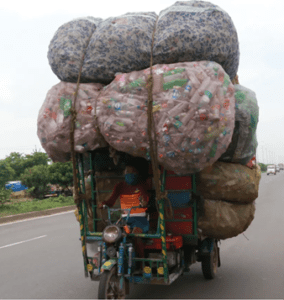
Adding plastic to roads appears to slow their deterioration, minimises potholes and improves surface flexibility as well. It also saves three tonnes of carbon dioxide for every kilometre of road. And there are economic benefits too, with the incorporation of plastic resulting in savings of roughly $670 (£480) per kilometre of road. Plastic-tar Road can withstand both heavy load and heavy traffic, it is not affected by rain or stagnated water. The UK government recently announced £1.6m for research on plastic roads to hel fix and prevent potholes. Unlike the plastic-tar roads laid in India, the UK and elsewhere, Plastic Road doesn’t use any bitumen at all. Each square metre of the plastic cycle path incorporates more than 25kg of recycled plastic waste, which cuts carbon emission by up to 52% compared to manufacturing a conventional tile-paved bike path. Ordinary roads, tyres and car brakes are already known to be a major source of micro plastic pollution. Koudstaal says that plastic-containing paths do not produce more micro plastics than a traditional road, as users don’t come into direct contact with the plastic. The bike paths include a filter that cleans out micro plastics and ensure rainwater infiltrates into the ground cleanly.
In addition to plastics now appearing on roads, they are also now going on bricks. These bricks have been made from foundry dust (75%) and waste plastic (25%). They are very cost effective, lighter and 2.5 times stronger than clay bricks. There is no use of water in the making of these bricks which means more water is saved during the construction process. Sand used to make metal castings is cleaned and reusable in the same process (Green sand reclamation process). Rhino bricks can sustain about 14-15 kg per cm square because of the compressive strength of the ingredients compared to 3.5-7 kg per cm square of conventional clay bricks. Rhino bricks can also retain their shape and strength even if a hole were drilled in the middle. The manufacturing process releases zero emissions into the environment, and the bricks are ready for use after being rested for 30 minutes.
REFERENCES
https://www.bbc.com/future/article/20200819-why-plastic-waste-is-an-ideal-building-material
https://www.bbc.com/future/article/20210302-could-plastic-roads-make-for-a-smoother-ride
https://www.thebetterindia.com/233190/plastic-waste-bricks-cheap-low-cost-purchase-features- recycle-engineer-architect-anand-gujarat-ang136/