Ocean waste, damaged marine life, barges adrift with unrecycled plastics and clogged landfills—all are indicative of the plastics problem—or what might be better described as a plastics contradiction. With waste piling up, there has been a surge in interest for more traditional packaging alternatives, those materials that plastics replaced over the last few decades—paper, glass and metals. All these plastic-free options have a significantly higher carbon footprint than most plastics, even when substantial recycled material is used. The main selling points of Plastic—inexpensive, easily coloured and shaped, food safe and lightweight—mean that people do not treat it with the reverence deserving of such a revolutionary engineered material. This, in turn, explains its dominance in our throwaway, convenience culture and the resulting damage it is doing.
Micro plastics found in the ocean are predominantly from the breakdown of plastic waste already there, but the wear of car tires and washing of synthetic clothing provide large amounts as well. The current push for a plastic-free future does not mean all plastics: bioplastics tend to be given a free pass, but this is where it gets a little complicated. Some bioplastics degrade relatively quickly in the ocean; some are compostable; some need an industrial facility to do so rapidly; and some are as durable as the foamed polystyrene food packaging that is likely to last 300 years before breaking down fully. In other words, bioplastic does not always mean biodegradable. Cellophane, which is synthesized from wood, and used to package candies, tea and other food products. Even metallizing the cellophane to create a light and oxygen barrier does not stop it from being compostable.
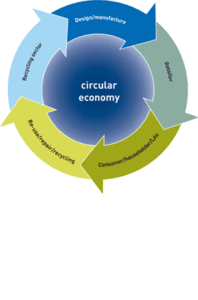
Another class of plastics that are quickly degradable in seawater are polyhydroxyalkanoates (PHAs) and polyhydroxybutyrate (PHBs) derived from bacteria that feed on sugary sources such as corn. Resins are being developed for a range of single use as well as durable applications. The current challenge for PHA/PHB bioplastics is the price of sugar, since it takes four pounds of sugar to produce one pound of the plastic. The plastic has a base-level cost that is higher than all the commodity plastics it is competing against. Recent advances in raw material compatibility have enabled NAFIGATE4 to produce a version of this plastic, known as P3HB, from the microbial fermentation of waste cooking oil, removing the high cost of the raw material entirely. Petrochemical producers are among the most sophisticated in terms of managing in-process hydrocarbons flows, using a mix of products and technologies.
Incineration will have permanent consequences for the environment and move us further away from the practices and ideals of a circular economy, where waste and climate impact are reduced. When considering the option of incineration, local leaders will be tempted by the quick-fix nature of burning waste. In Detroit, an incinerator financed with debt ended up costing taxpayers $1 billion over the course of 30 years. When discarded plastic is burned, carbon emissions are released (along with other pollutants), and the product is destroyed. The flow of materials from extraction to manufacturing to use is responsible for 50% of greenhouse gas emissions; a circular loop for plastics could reduce greenhouse emissions by as much as 37%.